Galvanic (Sacrificial) Anodes for Corrosion Prevention
MATCOR manufactures and supplies galvanic anodes—also known as sacrificial anodes—for a wide range of cathodic protection applications. These anodes provide simple, cost-effective protection for buried or submerged metal assets exposed to corrosive environments.
Our product line includes magnesium, zinc, and aluminum anodes, available in multiple configurations to meet your project needs.
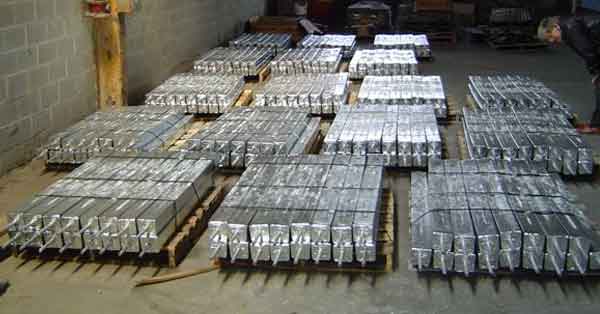
Product Overview: Galvanic Anode Types and Options
We offer several metal types and configurations tailored to t specific environments:
Magnesium Anodes
- High potential (-1.75V/CSE) for high-resistivity soils and freshwater
- Standard potential (-1.55V/CSE) for moderate-resistance environments
- Commonly packaged with ion-rich backfill (gypsum/bentonite) to enhance performance
- Lower efficiency (~50%)—higher consumption rate
Zinc Anodes
- Ideal for brackish and seawater
- Highly efficient (90-95% utilization factor)
- Packaged with backfill for soil applications
- Not suitable for high-temperature or high-resistance environments
Aluminum Anodes (Including Galvalum III)
- Designed for marine and offshore environments
- Efficiency: 85–95%
- Galvalum III offers high performance with a potential of -1.1 to -1.15V/CSE
Galvanic Anode Configurations
MATCOR’s offers anodes in multiple l forms for flexible installation:
- Bare metal anodes – Direct attachment for certain marine/industrial applications metal-to-metal contact is required
- Packaged anodes in backfill – Ideal for underground installations
- Anodes with mounting straps – Easy to attach to pipes, ships, or tanks
- Ribbon anodes – Flexible for long or irregular surfaces
- Rod and special-shaped anodes – Custom-designed for unique installations
Looking for alternatives to galvanic anodes? Explore our impressed current anodes.
Applications
MATCOR supplies galvanic anodes for a wide range of corrosion prevention needs:
- Underground pipelines and infrastructure
- Marine structures: docks, jetties, ship hulls, offshore platforms
- Tanks and vessels: internal protection
- Industrial systems in harsh, corrosive environments
Advantages of Galvanic Anodes
- Operate without external power
- Low maintenance and long-lasting
- Reduce stray current interference
- Ideal for remote or hard-to-access locations
- Lower total cost of ownership in many applications
What are Galvanic Anodes?
Galvanic anodes are metallic components used in cathodic protection (CP) systems to prevent corrosion. They work by sacrificing themselves—corroding in place of the protected structure.
Galvanic anodes generate protective current naturally, using the difference in electrochemical potential between the anode material and the structure being protected. Unlike impressed current systems, they require no external power source and are valued for their simplicity and reliability.
While the terms galvanic anode and sacrificial anode are often used interchangeably, both describe the same protective principle: the anode corrodes instead of your asset.
How Galvanic Anodes Work
When connected to a metal structure, galvanic anodes create a voltage differential that causes current to flow from the anode to the structure. This process prevents corrosion on the protected metal surface.
FAQ—Galvanic Anodes Explained
Get beyond the basics with the answers to the most common questions we hear. Have a question not answered here? Ask our experts!
Protect your assets for the long-term. Contact MATCOR today for all your project needs!
Yes, galvanic anodes are commonly called sacrificial anodes because they degrade over time while protecting the structure. The term sacrificial emphasizes how the anode corrodes (sacrifices itself) instead of the protected metal.
While galvanic anodes offer simplicity and reliability, they also have limitations:
* Lower driving force compared to impressed current systems
* Shorter service life in certain applications
* May not be suitable for some acidic environments
* Not ideal for high-resistance environments above 10k ohm-cm
* Difficult to adjust output once installed
Because galvanic anodes cannot be adjusted after installation, they require precise system design to ensure they provide just the right amount of protection for the intended lifespan.
Cathodic protection is an electro-chemical process that follows Ohms law (V=IR), where V (voltage) = I (current) x R (resistance).
In a galvanic anode system, the voltage difference between the anode and the protected structure is known as the driving potential. This difference determines how much current flows in the system, directly influencing the level of corrosion protection.
As galvanic anodes protect a structure, they undergo an oxidation reaction that transforms the metal anode into a metallic oxide. While metal itself is not destroyed, it gradually degrades and dissolves into the surrounding environment, reducing the anode’s mass over time.
The rate at which a galvanic anode is consumed in determined using Faraday’s Law, which quantifies the relationship between the number of metal atoms oxidized and the electrons transferred Consumption rates vary by anode type and are typically measured in kg/amp-yr (lbs/amp-yr).
Galvanic anodes are not 100% efficient—some of their mass is lost due to impurities, self-corrosion, or uneven degradation. The utilization factor, which varies by anode type, is essential when designing a CP system to ensure adequate lifespan and performance.
Magnesium anodes are available in two common alloys: high potential and standard.
* High potential magnesium anodes (-1.75V/CSE) are used in high-resistivity environments, such as fresh water and soil.
* Standard magnesium anodes(-1.55V/CSE) provide moderate protection and are more commonly used in lower-resistivity environments.
* Magnesium anodes typically have a lower efficiency (~50%), meaning they consume more quickly than other galvanic anodes.
Zinc anodes have a lower natural potential (-1.1V/CSE) than magnesium, making them best suited for low-resistance environments such as brackish and sea water applications.
* Zinc anodes are highly efficient (with a 90-95% utilization factor).
* They are not recommended for high-resistance or high-temperature environments.
In soil applications, zinc anodes are often packaged with gypsum-bentonite backfill to improve performance.
In the image below, steel galvanic anodes are used to protect the steel pipe piles for a jetty under construction.
Galvalum III is a high-performance alloy (alluminum/indium/zinc) used in marine environments.
* It has a higher potential than standard aluminum anodes (-1.1 to -1.15V/CSE).
* It is commonly used on offshore pipelines, ship hulls, and marine structures.
* Aluminum anodes have a utilization efficiency of 85-95%, making them highly effective in seawater applications..
Unlike impressed current systems, galvanic anodes do not have an external power supply for monitoring. This makes it difficult to monitor the anode system performance.
If monitoring is required, then it is common to have the anode connected to the structure through a test station equipped with a shunt. This arrangement provides access to measure the anode system’s current output without having to dig up the anode to structure connection.
For the most part, however, these galvanic systems are often installed with no significant monitoring provisions and are run until failure. This install-and-forget feature is simultaneously both an advantage and a disadvantage of galvanic anode systems.
Backfill materials help improve anode performance, especially in soil applications. The most common mixtures include:
* Magnesium anodes: 75% gypsum, 20% bentonite, 5% sodium sulfate
* Zinc anodes: a 50% gypsum, 50% bentonite