Improve Safety by Reducing the Impact of External Corrosion on Pipelines
External Corrosion Direct Assessment (ECDA) is a structured process that assesses and reduces the impact of external corrosion on pipeline integrity and improves safety. ECDAs proactively prevent corrosion defects from growing to a size that would ultimately impact a pipeline’s structural integrity by:
- Identifying corrosion activity
- Enabling the repair of corrosion defects
- Facilitating corrosion source remediation
ECDA is a continuous improvement process. Through regular assessments, pipeline operators can identify and address locations where corrosion has occurred, is occurring, or may occur. The external direct assessment of a pipeline involves four phases:
4 Phases of External Corrosion Direct Assessments
1—Pre-Assessment
In the pre-assessment phase, corrosion technicians and engineers conduct a detailed right-of-way (ROW) inspection and collect all pipeline operating data. This phase also involves identifying High Consequence Areas (HCAs) and their classification based on the surrounding environment, such as the number of structures within a specific distance from the pipeline.
2—Indirect Inspection
The indirect assessment field crew works under the direction of a MATCOR Pipeline Integrity Manager and Engineering Manager. The crew has all the required “Operator Qualifications” and operates under the guidance of your project manager.
The indirect testing phase includes two or more of the following testing methods:
- Close Interval Surveys (CIS): Measures cathodic protection system efficacy by taking potential readings every two and a half feet along the pipeline.
- Direct and Alternating Current Voltage Gradient Surveys (DCVG/ACVG): Assesses the pipeline condition and identifies holidays (abnormalities) in the coating.
- Pipeline current mapping (PCM): Shows the flow of electricity, helping to identify coating anomalies and stray currents
- Soil Resistivity Testing: Measures the corrosivity of the soil at pipeline depth.
- Soil pH Testing: Determines the acidity or alkalinity of the soil, which impacts the rate of corrosion.
Evaluating soil resistivity and pH enables pipeline operators to identify areas more prone to corrosion and implement targeted protective measures.
Indirect Assessment Levels of Severity
Tool | Severity of Measurement Amplitude Change of Indication | |||
None | Minor | Moderate | Severe | |
CIS | Small dips (<100mV) in off potentials AND off potential meet criteria | Small dips (100 to 150 mV) in off potentials AND off potentials meet criteria | Medium dips (>150 mV to 300 mV) in off potentials OR off potentials do not meet criteria | Large dips (>300 mV) in off potentials and off potentials both do not meet criteria |
DCVG | IR 25% or less | >25% to 50% IR | >50% to 75% IR | >75% to 100% IR |
ACVG | 25 dB or Less | >25 dB to 50dB | >50% dB to 75 dB | >75 dB |
Depth of Cover | >36″ | >24″ to 36″ | >12″ to 24″ | 12″ or less |
3—Direct Assessment
After analyzing and reviewing data from the indirect assessment methods, the ECDA contractor and operator identify, specific locations for direct examination. This phase involves:
- Performing confirmatory excavations to access the pipeline
- Physically inspecting pipeline coating condition
- Evaluating cathodic protection system condition
- Identifying pipeline defects and corrosion damage
- Assessing soil characteristics such as resistivity and pH at pipeline depth
4—Post Assessment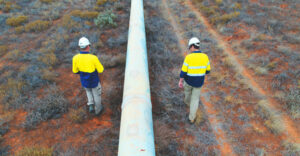
Post-assessment reports compile data from all phases of ECDA, documenting areas of concern, the condition of the coating, and any external damage to the pipeline. This comprehensive documentation is crucial for making informed decisions about pipeline maintenance and safety enhancements.
PHMSA Regulations and Regular Assessments
The Pipeline and Hazardous Materials Safety Administration (PHMSA) regulates the schedule and standards for ECDA.
PHMSA requires assessments cyclically to ensure ongoing pipeline integrity and safety. Compliance with these regulations is crucial. Failure to conduct ECDA assessments on the mandated schedule can have severe consequences:
- Fines and Penalties: Pipeline operators can face significant fines and penalties for non-compliance with PHMSA regulations.
- Pipeline Integrity Risks: Delayed or missed assessments increase the risk of undetected corrosion, which can lead to pipeline failures and environmental hazards.
- Operational Interruptions: Non-compliance may require operators to conduct emergency inspections or repairs, leading to operational interruptions and increased costs.
- See 49 CFR 192.925 for more information on PHMSA regulations surrounding ECDA parameters
Benefits of ECDA
ECDA provides an in-depth overview of the health of a pipeline from an external standpoint. Regular assessments ensure continuous monitoring and maintenance, preventing significant corrosion issues.
Unlike inline inspection (ILI), ECDA does not require shutting down the pipeline, making it a more efficient and less costly option for many pipeline operators.
Alternatives to ECDA
The primary alternative to ECDA is inline inspection (ILI) using a smart pig. However, not all pipelines are equipped for pigging, making ECDA a more suitable assessment method for pipelines without the necessary ILI launcher and receiver infrastructure.
MATCOR’s ECDA Expertise
With 50 years of experience, MATCOR offers:
- Expertise in all types of cathodic protection systems
- Experience in testing, installing and maintaining cathodic protection systems worldwide
- A team of highly qualified AMPP certified corrosion engineers and technicians
- Full turnkey solutions, including design, manufacture, construction and installation, commissioning, ongoing maintenance, and project management
As a full-service cathodic protection and corrosion control provider, MATCOR’s mission is to solve your corrosion problems and provide you with superior quality service. We are ready to assist with your corrosion engineering and field service needs.
ECDA Project Cost
Your MATCOR ECDA project cost includes all labor, equipment (including all necessary interrupters), per diem, final reporting, and materials to complete your project. Traffic control and other ancillary expenses are additional if required.
For more information, to ask a question or get a quote, please contact our team of corrosion experts. We will respond by phone or email within 24 hours. For immediate assistance, please call +1-215-348-2974.
Contact a Corrosion Expert