This article discusses the most common soil resistivity testing method and provides some guidelines for properly collecting sufficient data for the cathodic protection system designer.
One of the most important design parameters when considering the application of cathodic protection for buried structures is the resistivity of the soil. Soil resistivity testing is an important consideration for assessing the corrosivity of the environment to buried structures. It also has a tremendous impact on the selection of anode type, quantity, and configuration. Thus, it is critical that the CP designer have accurate data on the soil conditions at both the structure and at any proposed anode system locations. The lack of sufficient soil resistivity data can render a cathodic protection system (CP system) design ineffective and can result in costly remediation efforts during commissioning.
Soil Corrosivity
Soil resistivity is the principal diagnostic factor used to evaluate soil corrosivity. When performing soil resistivity testing, there are numerous factors that can be assessed, including soil composition, moisture content, pH, chloride and sulfate ion concentrations, and redox potential. These are all common components of a lab or in-situ soil testing program and all have an impact on soil resistivity. While a comprehensive soil testing program may be warranted, especially when performing failure analysis, for most environments the soil resistivity testing data provides an outstanding basis for assessing soil corrosivity. Below is a typical chart correlating soil resistivity with soil corrosivity.
Soil Resistivity (ohm-cm) | Corrosivity Rating |
>20,000 | Essentially non-corrosive |
10,000 to 20,000 | Mildly corrosive |
5,000 to 10,000 | Moderately corrosive |
3,000 to 5,000 | Corrosive |
1,000 to 3,000 | Highly corrosive |
<1,000 | Extremely corrosive |
SOURCE: Corrosion Basics: An Introduction, NACE Press Book, 2nd edition by Pierre Roberge
Soil Resistivity Testing
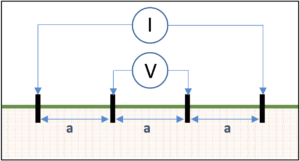
While there are several methods for measuring soil resistivity, the most common field testing method is the Wenner four-pin method (ASTM G57). This test uses four metal probes, driven into the ground and spaced equidistant from each other. The outer pins are connected to a current source (I) and the inner pins are connected to a volt meter (V) as shown in Figure 1.
When a known current is injected in the soil through the outer probes, the inner probes can be used to measure voltage drop due to resistance of the soil path as current passes between the outer probes. That resistance value R can then be converted into a soil resistivity value with the formula: ρ=2×π×a×R where “ρ” is measured in ohm-cm and “a” is the spacing of the pins in cm. This value represents the average soil resistivity at the depth equivalent to the spacing of the probes so if the probes are spaced 5 foot apart, the value derived would be equivalent to the average soil resistivity at 5 foot depth.
For cathodic protection system design, it is common to take multiple soil resistivity measurements using this methodology with various probe spacings. For shallow anode placement, it is usually sufficient to take reading readings at 2.5 ft, 5 ft, 10 ft, 20 ft, 25 ft. For deep anode applications, soil resistivity measurements may be recommended at much deeper depths corresponding with the anticipated depth of the deep anode system.
Layer Effects
It is important to note that the soil resistivity values generated from the four pin testing represent the average soil resistivity from the earth surface down to the depth, and each subsequent probe spacing includes all of the shallow resistance readings above it. For cathodic protection design purposes, it is often necessary to determine the resistance of the soil at the anode depth by “subtracting” the top layers from the deep readings. This process of “subtracting” the top layers requires some form of computational adjustment. One popular approach is called the Barnes method which assumes soil layers of uniform thickness with boundaries parallel to the surface of the earth. If the measured data indicates decreasing resistance with increasing electrode spacing, this method can be used to estimate the layer resistivities.
The resistance data (R) values should be laid out in a tabular format and then converted to conductance which is simply the reciprocal of the resistance value. The change in conductance is then calculated for each subsequent spacing. That value is then converted back to a layer resistance value by taking the reciprocal of the change in conductance. Finally, the layer resistivity is calculated using ρ=2×π×a×R.
For the Barnes analysis below, the data shows that a low resistance zone exists between 60m depth and 100m depth.
TEST DATA | BARNES ANALYSIS | ||||
Spacing a |
Resistance (ohms) |
Conductance 1/R (Siemens) |
Change in Conductance (Siemens) |
Layer Resistance (ohms) |
Layer Resistivity |
20 | 1.21 | 0.83 | — | 1.21 | 152 |
40 | 0.90 | 1.11 | 0.28 | 3.57 | 441 |
60 | 0.63 | 1.59 | 0.48 | 2.08 | 264 |
80 | 0.11 | 9.09 | 7.5 | 0.13 | 17 |
100 | 0.065 | 15.38 | 6.29 | 0.16 | 20 |
120 | 0.058 | 17.24 | 1.86 | 0.54 | 68 |
Soil Resistivity Testing Equipment Considerations
Electrically speaking, the earth can be a rather noisy environment with overhead power lines, electric substations, railroad tracks, and many other sources that contribute to signal noise. This can distort readings, potentially resulting in significant errors. For this reason, specialized soil meter equipment that includes sophisticated electronic packages capable of filtering out the noise is critical when taking soil resistivity data.
There are two basic types of soil resistivity meters: high-frequency and low-frequency meters.
High-frequency Soil Resistivity Meters
High-frequency meters operate at frequencies well above 60 hz and should be limited to data collection of about 100 feet in depth. This is because they lack sufficient voltage to handle long traverses and they induce noise voltage in the potential leads which cannot be filtered out as the soil resistivity decreases and the probe spacing increases. These are less expensive than their Low-Frequency counter parts and are by far the most common meter used for soil resistivity testing. For CP design purposes, these are frequently used to assess soil corrosivity and for designing shallow anode applications.
Low-frequency Soil Resistivity Meters
Low-frequency meters generate pulses in the 0.5 to 2.0 hz range and are the preferred equipment for deeper soil resistivity readings as they can take readings with extremely large probe spacings. Some models can operate with spacings many thousands of feet in distance. These models typically include more sophisticated electronics filtering packages that are superior to those found in high-frequency models. For CP designs involving deep anode installations, a low-frequency meter is the preferred equipment to provide accurate data at depths below 100 ft.
Field Data Considerations
When collecting accurate soil resistivity data for cathodic protection system design, it is important that the following best practices are taken into consideration to avoid erroneous readings:
- Suitability of the testing location. The use of the Wenner four pin testing method requires sufficient open area to properly space the pins to collect data to the depths necessary. For deep anode cathodic protection systems this would require a minimum of three times the anticipated anode system depth.
- Avoidance of buried piping and other metallic objects. The presence of any buried metallic structures (piping, conduit, reinforced concrete structures, grounding systems, etc…) provides low current paths that could cause a short-cutting effect that would distort the resistance readings and yield an erroneous soil resistivity reading.
- Depth of the probes. It is important that the probes are properly inserted into the earth. For shallow resistivity readings, probes that are driven too deep can impact the shallow readings. Ideally, the pins should be no deeper that 1/20th of the spacing between the pins and no more than 10 cm (4 inches) deep.
- Avoid areas of high electrical noise. Soil testing should not be performed directly under high voltage transmission systems or near other outside sources of current in the soil such as DC light rail systems.
- Accurately record the test location and conditions. It is important that the location of the testing is accurately recorded along with the soil conditions and temperature at the time of testing. Testing should not be performed in frozen soil, or during periods of extreme drought or abnormally wet conditions.
Summary
Soil resistivity testing with accurate collection of data is the best indicator of the corrosivity of the soil for buried metallic structures and has a significant impact on the design of cathodic protection systems. The most common test methodology for field collection of soil data is the Wenner four pin method. When properly collected, and using appropriate analytical techniques, the soil resistance field data can provide an accurate assessment of soil resistivity values for use in designing an appropriate cathodic protection system.
Learn about MATCOR Soil Resistivity Testing Services
Very good , clear and simple explanation
My husband would like to purchase a property where he can have a building built. I agree with you that the application of cathodic protection of buried structures must be used for the resistivity of the soil. Better yet, we’ll just hire a commercial erosion service so we’ll know if the soil is in good shape.
Rachel – Thank you for your comment. As a general rule, soil corrosivity is not a significant concern for most building structures. There are plenty of other soil concerns including structural stability, environmental assessments, etc… that should be performed by companies that specialize in these assessment prior to commercial or residential property development. Best wishes! Ted Huck, Director of Manufacturing & QA, MATCOR, Inc.
Hi,
I am writing from Tekfen Construction. Now we are working one Saudi Aramco project. Based new systems that you proposed , we have some query. If you reply, we will appreciate.
1. If previous resistance is same with next one, how we calculate change in conductance ( looks 0)?
2. If previous conductance (1/R) is higher than next one, how we calculate change in conductance ?
3. What will be layer resistance for 2 questions?
Dear Osman:
Based on your question, it seems as though you are trying to calculate soil layer resistivity using the Barnes layer calculations. The Barnes layer method uses very broad assumptions:
1. The horizontal layers are homogenous
2. The thickness of the horizontal layers are even and level (parallel) with the surface of the earth
3. The resistance readings that you collect are a result of the test current going deep into the earth and traveling through all of the target layers
If the target soil layers are not homogenous, are not level, or vary in thickness, then the readings will be affected.
Also, standard soil resistivity meters – which operate on low voltage and high frequency – are only reliable for electrode spacings up to 15 meters in most soils, and a maximum of 30 meters. Many of these meters do not have the sensitivity to measure low resistances accurately. I have found this to be a major source of error.
Hope this information helps.
Best regards,
Kevin Groll
Engineering Manager
MATCOR, Inc.
Dear Sir,
Thank you so much your explanation and review my knowledge .
Best wishes,
Taufik
do you have a method for non-uniform thickness layers…we ran “a” spacing of 1, 2, 5 and 10 ft (looking at really shallow variations)…
Dear John,
Thank you for your inquiry. The Barnes layer method is a theoretical construct based on a range of assumptions and is useful for extrapolating resistivities at depths where core sampling may not be practical. For a more detailed understanding of this methodology, we would refer you to https://onlinepubs.trb.org/Onlinepubs/hrbbulletin/65/65-002.pdf . If you are looking at shallow variations as your post suggests, it should be quite feasible to collect actual soil samples at each of those depths and use a soil box to measure in-situ resistivity data.
Hope this is helpful. Let us know if we can be of further assistance.
MATCOR, Inc.
The 68 ohm-m layer resistivity at 110m spacing is incorrect. All other values are correct. From my calculation, the correct value is 34 ohm-m and not 68 ohm-m as shown in the example. Kindly cross-check your result.
Thanks
Udeme,
We appreciate your input on our article regarding soil resistivities and Barnes Layer calculations. There were some errors in the results table for the sample calculations, and we have updated the table. Please continue to provide your input and comments as we strive to make the MATCOR website a great technical resource for our customers and for the industry in general.
Best regards,
MATCOR, Inc.
what is the proper or recommended soil resistivity for magazines?
Dear Elijah Nchidzi,
Thank you for your inquiry. Magnesium anodes are typically used in soil applications with resistivities ranging from 2000 oh-cm to 7500 ohm-cm. Soil resistivities that are higher than 7500 ohm-cm often require a large quantity of anodes to reduce the overall anode to earth resistance so that sufficient current can be discharged to protect the intended structure. Conversely, soil resistivities below 2000 ohm-cm often result in high current discharge and shorter anode life. Of course, there are exceptions to this general guideline, and anytime we are considering galvanic anodes it is critical that a thorough design be performed, as there is no “volume” switch on a galvanic anode to increase (or decrease) the current output.
We hope this is helpful. Please let us know if you have further questions.
Best regards,
MATCOR, Inc.
If soil resistivity is found to be 66 ohms – cm how can I incorporate this result in designing of CP system based on HSCI Anodes for buried section of piles.
Dear Raza,
We thank you for the question you posted on our website. Soil resistivity value is used to determine the cathodic protection current requirement and ground bed resistance calculations for your ICCP system.
Best regards,
MATCOR, Inc.
Dear Raza,
While working on a grounding design I encountered a peculiar problem.
I know from Geotech data that the site I am working on has hard rock from 5 feet depth to 15 feet depth.
The resistivity of rock is supposed to be 10000 Ohm-m.
However with Barnes calculations for 0-5 feet layer the resistivity is 153 Ohm-m; 5 to 10 feet layer it is 194 Ohm-m and 5 to15 feet layer it is 59 Ohm- m.
Why Barnes layer resistivity is not comparable with actual rock resistivities of 10000 Ohm-m
Regards
rg
Dear Mr. AarGee,
Thank you for your inquiry. Without understanding the equipment and the data methodology used to collect the data being input into the Barnes layer calculations, it is not possible for us to comment on the results. If accuracy of the measurements that you are taking vary significantly from what you know to be true in the environment you are testing, it would appear that something was not performed during the field testing. We would suggest that you review your processes and the equipment that you are using and retest the area in question.
Best regards,
MATCOR, Inc.
Dear,
Nice Explanation..
thank you,
regards,
kannan