Cathodic Protection for Underground Piping Overview
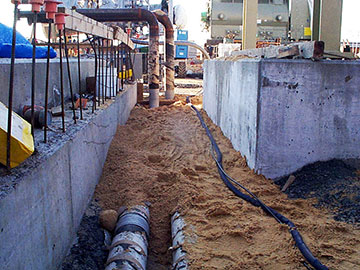
This article reviews 3 steel pipe corrosion protection methods utilizing cathodic protection.
Cathodic protection, when applied properly, is an effective means to prevent corrosion of underground plant piping. For many underground applications, such as pipelines, cathodic protection system design is relatively straightforward. Plant and facility environments, however, are not simple applications. Plants have congested underground piping systems in a tightly spaced footprint. The presence of copper grounding systems, foundations with reinforcing steel embedded in concrete, conduit, utility piping and structural pilings (either bare or concrete with reinforcing steel) can greatly complicate the task of designing a pipe cathodic protection system.
For simple plant facilities, it is possible to isolate the piping and utilize a conventional galvanic corrosion prevention system. This works only if the plant piping is electrically isolated from other underground structures for the life of the facility. For most plant and facility applications, it is not practical to isolate the piping from the grounding system for the life of the facility. In these cases an impressed current anode system is the only alternative.
3 Methods of Cathodic Protection for Underground Piping and Structures
There are three basic approaches to cathodically protect underground piping and structures using impressed current anodes.
-
Deep Anode
One method is the deep anode in which high current capacity anodes are installed from the structure in a deep hole drilled vertically 150+ feet deep. This is analogous to lighting a football field with floodlights.
-
Shallow Anode or Distributed Anode Bed
Another method is to use a shallow ground bed anode design where many smaller capacity ground bed anodes are spaced near the intended structures – analogous to street lamps lighting a street.
-
Linear Anode
The third method is to place a linear anode parallel to and in close proximity to the piping to be protected discharging current continuously along its length – similar to fiber optic lighting.
This technical bulletin details the advantages of using the linear anode approach for new plant construction projects to protect buried piping in a congested environment. This approach provides the most effective solution both technically and commercially.
Pipe Cathodic Protection Design Issues for Plants & Facilities
Electrical Isolation in a Congested Plant Environment
Electrical isolation is a major concern when designing a CP system for any plant or facility application. Isolating a single cross country pipeline segment from point A to point B is achieved rather simply through the use of electrical isolation flanges/isolation joints that the pipeline operator maintains and tests regularly. The realities of power plant piping networks, on the other hand, significantly complicate electrical isolation. By code, everything above grade in a plant must be grounded, yet it is common to see pipe cathodic protection systems designed based on isolation of the buried piping. Even if electrical isolation is achieved during the plant construction, maintaining electrical isolation over the life of the facility may not be realistic. Given the speed and complexity with which new plants are erected, achieving electrical isolation during construction is no simple task. Once installed, electrical isolation flange kits require regular monitoring and periodic replacement that often does not occur. Piping modifications and other plant maintenance activities can also result in an inadvertent loss of electrical isolation. Cathodic protection for underground piping that relies on electrical isolation should be avoided for plant applications.
Current Distribution – a Critical Issue in Pipe Cathodic Protection Design
Another critical issue that must be properly considered during the design of a CP system for plant applications is the highly congested underground environment and the challenges of achieving thorough current distribution. Buried piping is often located in congested underground areas in close proximity to grounding systems, foundations with reinforcing steel, pilings systems, metallic duct banks and other structures that can shield current from the piping systems that are the intended target of plant cathodic protection systems. It is virtually impossible to assess where current will go in a plant environment – the more remote the anode source, the more difficult it is to assure appropriate current distribution.
Stray Current
When discussing current distribution, it is also important to discuss the potential for stray current. For grounded systems, current that is picked up by other buried metallic structures is merely current that is wasted and not available to protect the intended buried piping structures. For isolated metallic structures, such as foreign pipelines, ductile iron piping systems, and nearby facilities or structures, stray current may be a significant concern. Stray current problems occur when current is picked up on an isolated structure and later discharges off that structure and back to a grounded structure. At the location where stray currents discharge, rapid corrosion may be inadvertently induced on the isolated structure.
The Case for Linear Anode Cathodic Protection System Design
The linear anode solution consists of long runs of linear anode installed parallel and in very close proximity to the piping being protected. The current output is kept very low and is generally consistent across the entire system. A linear anode is in effect a distributed system with an infinite number of anodes spaced continually. This system provides the best technical cathodic protection solution and minimizes the current output required as follows:
- Does not require electrical isolation.
Because the linear anode is closely located next to the piping being protected, electrical isolation is not a significant concern. The anode is “closely coupled” to the piping and operates with a very low anode gradient that minimizes any losses to nearby structures including grounding. - Assures good current distribution as the anode runs parallel to the piping being protected.
The linear anode cathodic protection system design eliminates any requirement for supplemental anodes to address areas where remote anodes may be shielded after the CP system is commissioned. Wherever the piping goes, the linear anode follows in the same trench. This also makes it very easy to adapt the design during piping revisions that may change the piping system routing as the plant construction proceeds. - Eliminates risks of stray current.
Close proximity to the piping being protected significantly limits current losses to other structures and virtually eliminates shielding and stray current concerns. This also significantly reduces the total current requirements for the system, reducing the rectifier requirements. - Access issues – the linear anode is installed in very close proximity to the piping that is to be protected.
This minimizes the risk of third party damage and reduces trenching required for buried cable. If installed in conjunction with the piping, the anode can be placed in the same trench as the piping affording the anode protection by the piping itself from external damage. This is a very cost effective cathodic protection installation when installed concurrently with the piping. - Ease of installation – when installed alongside the piping as the piping is being installed, the installation is simply a matter of laying the anode cable in the trench.
Our experts are happy to answer your questions about cathodic protection for underground piping.
Contact a Corrosion Expert