Internal pipeline corrosion is a significant challenge for maintaining pipeline integrity, particularly during construction or after hydrotesting. Vapor Corrosion Inhibitors (VCIs) provide a targeted solution for protecting internal pipeline surfaces and mitigating corrosion risks.
For a comprehensive overview of pipeline corrosion challenges, visit our Pipeline Corrosion and Prevention—A Comprehensive Guide.
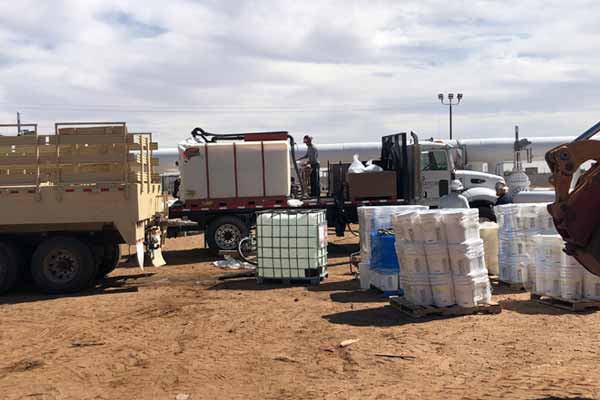
The Challenge of Pipeline Internal Corrosion
Internal corrosion occurs when contaminants such as water, oxygen, and bacteria interact with the metal surfaces inside a pipeline. This risk is especially high after hydrotesting, a mandatory step for verifying pipeline integrity.
During hydrotesting:
- Residual moisture and bacteria often remain even after draining and drying, creating a highly corrosive environment.
- Hydrotesting introduces water into the piping to ensure there are no faulty welds and that the piping system can handle design pressure without leaks. Unfortunately, this testing can also introduce bacteria, which exacerbate corrosion risks.
Even with efforts to dry internal surfaces, residual moisture and contaminants can accelerate metal degradation, compromising long-term reliability.
How VCIs Work for Pipelines
VCIs are chemical compounds designed to protect pipelines by:
- Diffusing and adsorbing onto metal surfaces to create a molecular-level protective barrier.
- Blocking water and oxygen from reacting with the internal metal surface.
- Providing long-lasting protection for months or years, depending on application conditions.
For pipeline preservation applications, VCI chemicals are typically mixed with water into a slurry. This slurry is then pumped into the piping manifolds using a series of injection pumps and injection ports, delivered via hoses from multiple mixing tanks.
VCIs are particularly effective for hard-to-reach areas within pipelines, such as manifolds and intricate piping systems, where traditional methods may fall short.
For broader applications of this innovative technology, visit our Vapor Corrosion Inhibitors page.
VCI Case Study: West Texas Pipeline Reservation Project
MATCOR completed a significant preservation project at a newly constructed pipeline station in West Texas. Highlights of the project include:
- Injecting over 24,000 gallons of VCI solution into multiple above-ground manifolds after hydrotesting.
- Adding methanol (anti-freeze) to the slurry mixture to ensure freeze protection during winter.
- Successfully mitigating corrosion risks while the remainder of the construction continued.
This project demonstrated the effectiveness of VCIs in preserving pipeline integrity under challenging environmental conditions.
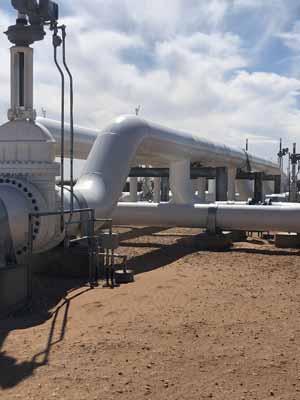
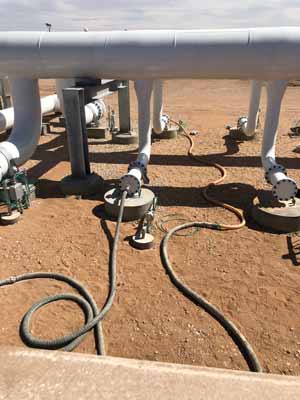
Enhancing VCI Effectiveness with Complementary Measures
VCIs are a powerful tool for internal corrosion prevention, but their effectiveness is maximized when used in conjunction with other measures:
- Reducing contaminants before pipeline entry: Ensures that corrosive agents are minimized, allowing VCIs to focus on existing risks.
- Internal pipeline cleaning: Removes residue and deposits that can interfere with VCI diffusion or create localized corrosion.
- Cathodic protection systems: Provide additional protection for pipeline areas not effectively reached by VCIs, such as crevices or air gaps.
By integrating VCIs with these measures, operators can create a comprehensive internal corrosion prevention strategy.
To get in touch with our team of cathodic protection experts for more information, to ask a question or get a quote, please click below. We will respond by phone or email within 24 hours. For immediate assistance, please call +1-215-348-2974.
Contact a Corrosion Expert