Pipelines are a crucial part of the US infrastructure, but they face a serious challenge: corrosion. This guide explains pipeline corrosion, the different types, and how to prevent it to avoid costly and dangerous failures.
The Problem of Pipeline Corrosion in the United States
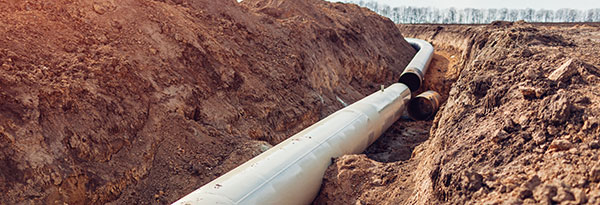
The United States has over 2,225,000 kilometers of pipelines transporting oil and natural gas. No other country comes close—Russia, in second place, has approximately 260,000 km. These pipelines are owned and operated by hundreds of companies and regulated by the US Department of Transportation’s Pipeline and Hazardous Materials Safety Administration (PHMSA).
Experts consider pipelines very safe—roughly 70 times safer than trucks1 and 4.5 times safer than rail2. However, many pipelines are at least 50 years old. This increases the risk of corrosion, which threatens their safety and reliability.
Why Pipeline Corrosion Prevention is Critical
Corrosion is a natural process where metal electrochemically reacts with the environment and deteriorates over time. Without regular maintenance and monitoring, this can lead to leaks or even pipeline ruptures.
The good news? Corrosion is completely manageable. By using the right technologies and maintenance practices, pipeline operators can manage corrosion and prevent failures.
Two Types of Pipeline Corrosion
Two primary types of pipeline corrosion exist.
- External Corrosion: Happens on the outside of the pipeline and causes approximately 8% of incidents.
- Internal Corrosion: Occurs inside the pipeline and accounts for approximately 12% of all incidents.
How to Prevent Pipeline Corrosion
Several strategies exist to prevent corrosion, depending on whether it occurs internally or externally.
Preventing External Corrosion of Pipelines
The two most effective methods to prevent external corrosion are:
- Pipeline coatings: These create a protective barrier between the pipeline and its environment. However, installation can damage them, and they can wear out over time.
- Cathodic protection systems: This method uses electrical currents to prevent the metal from corroding and requires frequent testing.
These methods work well, but require regular monitoring and maintenance to remain effective.
Preventing Internal Corrosion of Pipelines
Internal corrosion occurs when contaminants in the oil or gas being transported react with the pipeline. Common contaminants include oxygen, hydrogen sulfide, carbon dioxide, chlorides, and water. The severity of this corrosion is influenced by several factors, including:
- The concentration of contaminants
- The combination of different contaminants within the pipeline
- Operating pressure and flow velocity
- Pipeline design and holdup points
- Operating temperature
To effectively manage internal corrosion, operators must use a combination of assessment and prevention strategies, including:
- Reducing contaminants before they enter the pipeline.
- Applying internal pipeline coatings to create a protective barrier.
- Injecting inhibitors to minimize corrosion reactions.
- Frequent internal cleaning to remove residues.
The Role of Internal Corrosion Direct Assessment (ICDA)
Assessment is the foundation of effective corrosion management. Internal Corrosion Direct Assessment (ICDA) identifies high-risk areas and helps operators prioritize maintenance. ICDA is particularly valuable for:
- Evaluating risks based on contaminants, flow conditions, and pipeline design
- Identifying areas prone to localized corrosion
- Informing maintenance and repair strategies
Learn more about MATCOR’s Internal Corrosion Direct Assessment (ICDA) services.
The Role of Vapor Corrosion Inhibitors (VCIs)
VCIs are an advanced solution for preventing internal corrosion. They diffuse and bond with internal surfaces to create a protective barrier against water and oxygen.
VCIs are especially effective when used alongside other strategies, such as cathodic protection.
To explore the technology and benefits of VCIs across industries, visit our Vapor Corrosion Inhibitors guide.
For pipeline-specific applications of VCIs, see Pipeline Internal Corrosion Prevention with VCIs.
Keep Your Pipelines Safe from Corrosion
While pipeline corrosion is a serious issue, it can be effectively managed through proper monitoring and preventative measures. Whether facing internal or external corrosion, a strong integrity management program is essential to lowering the risk of failure.
Ensure your pipelines are fully protected from corrosion and explore our expert cathodic protection solutions and other comprehensive services.
Looking for a more in-depth explanation of cathodic protection? Learn more about cathodic protection systems.
1 propublica.org – Pipelines Explained: How Safe are Americas 2.5 Million Miles of Pipelines?
2 fraserinstitute.org – Pipelines are the Safest Way to Transport Oil and Gas
To get in touch with our team of cathodic protection and AC mitigation experts for more information, to ask a question or get a quote, please click below. We will respond by phone or email within 24 hours. For immediate assistance, please call +1-215-348-2974.
Contact a Corrosion Expert
It’s interesting to know how cathodic protection can apparently protect pipelines indefinitely but only in tandem with maintenance. I’m sure the amount of work done with these monitoring and maintenance would be less than if the pipes get changed or repaired periodically. I often wonder why it’s so rare for the pipelines around where I live get excavated for repairs. This article sheds some light on how resilient pipelines can be with the right protection.
Alice – Great comment regarding pipelines – it would be appropriate to point out that for many small diameter, low pressure distribution pipeline networks there has historically been a lot of these networks that have not been cathodically protected or well maintained. This is especially true in the water and sewer industries where there are a lot of pipelines that do not have cathodic protection and where failures are dealt with by digging up and repairing or replacing with plastic pipelines. For the higher pressure, larger diameter transmission type pipelines, the risks and costs associated with a pipeline failure are such that proper protection and maintenance is both a necessity and for oil and gas pipelines a regulatory requirement.
Ted Huck
Director of Manufacturing
MATCOR, Inc.