OH NO, My Anode Bed is Not Performing!
This article explores a deep anode system gone wrong and guidelines for properly sizing the system coke column.
Earlier this year, we received a call from a pipeline customer with whom we have a solid relationship.
Historically, they used graphite anodes for their deep anode installations. But over the past few years, they began trying the MATCOR Durammo® Deep anode System with success.
When one of their new Durammo anode installations started having strange operating data, it was time to get MATCOR on the phone pronto and figure things out.
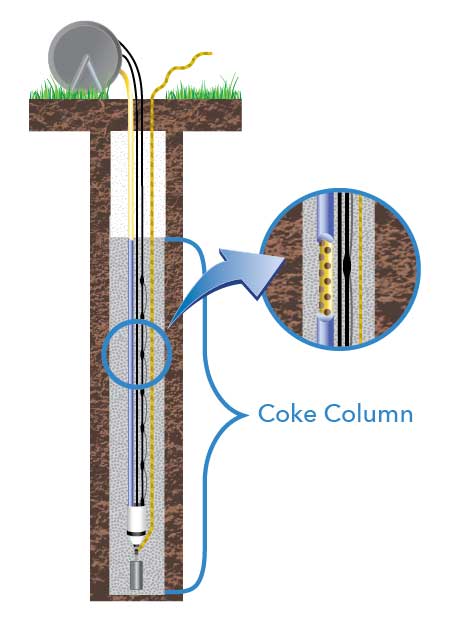
MATCOR reviewed the RMU operating data on the wayward installation and found that the data was indeed strange.
The DC output oscillated from periods of robust DC current output to periods of no discernible DC output. We also looked at the deep anode system design and noted the rather short coke column height. The height was only 100 ft of active anode in an 8-inch column. We sent a technician to the site to investigate.
First, we checked the installation and operation of the remote monitoring unit (RMU). Was a poor RMU connection causing intermittent good/bad data? This was not the case.
Next, we checked the continuity of the two anode lead cables. The Durammo® system has a top lead cable and a bottom lead cable. These two cables should be electrically continuous. In this installation, they checked out properly.
Finally, we checked the vent pipe for obvious issues.
Having confirmed that the spurious data was not the result of a poor RMU connection and that the anode system cabling appeared to be intact, we began to suspect that the problem was in the coke column and its immediate environment.
The Culprit? A Small Coke Column.
When we investigated further, we determined that the on-again, off-again readings could be the result of excessive gas generation into a rather small coke column. Both phenomena are heavily impacted by the anode system’s coke column to earth current density.
When the anode system generates more gas than can be exhausted through the vent pipe and diffused through the surrounding earth, gas molecules begin to accumulate between the column particles and at the anode to coke and coke column to earth interfaces. Gas is not electrically conductive, and with enough trapped gas in the column, the system resistance can quickly rise to a point that the anode system cannot overcome this resistance, and the current output drops quickly.
A short-term solution is to turn off the anode system for a period, allowing the gas to disperse inside the coke column and the system should return to normal operation. At least until the gas molecules build up again to block the anode system.
Coke Column to Earth Interface Current Density: The Magic Number
The magic number often cited for anode coke column to earth interface current density is 150mA/ft2. Anything above this number might cause problems. Below this number, history shows that the impact of gas blockage and drying out are generally minimal.
In our example, a 100 ft coke column with an 8-inch diameter hole means that any current output above 31 amps would be pushing that 150mA/f2 threshold.
The 150mA/ft2 current density assumes a high-quality, properly installed coke. This forms a well-compacted column that promotes electronic conduction and limits electrolytic conduction. A well-formed coke column is critical for anode systems using mixed metal oxide anodes, since MMO anodes have an inherently smaller surface area available to be in contact with the column.
It is unclear why the cp system designer recommended a short anode active length for this anode system – other than perhaps the cost saving of using less coke backfill.
While a shorter column does have a positive cost impact, the performance can become an issue, as was the case with this installation. Ultimately, this customer is planning a new Durammo® anode installation for this location with a significantly longer active area.
Need information or a quote for MATCOR deep anode systems? Please contact us at the link below.