This guide explores how Vapor Corrosion Inhibitors (VCIs) work, their diverse applications, and why they’re becoming a cornerstone of modern corrosion prevention strategies. Whether you’re in oil and gas, manufacturing, or aerospace, discover how VCIs can transform your approach to corrosion management.
Corrosion poses a significant threat to infrastructure and equipment across industries, from pipelines to storage tanks. VCIs offer a solution, using advanced chemical technology to protect metal surfaces and prevent costly damage.
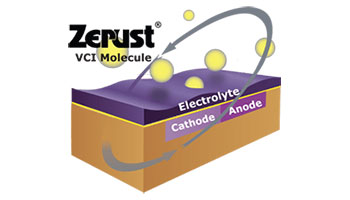
As a leader in the above-ground storage tank corrosion control industry, MATCOR has partnered with Zerust® Oil & Gas to provide innovative VCI solutions for customers seeking advanced corrosion mitigation strategies.
What are Vapor Corrosion Inhibitors?
Vapor Corrosion Inhibitors (VCIs) are advanced chemical compounds that prevent corrosion by diffusing through confined spaces and bonding with metal surfaces. This process creates an invisible yet highly effective barrier that blocks water, oxygen, and other contaminants from initiating degradation.
Key features:
- Create a passive oxide layer that inhibits chemical reactions
- Can be applied in various forms, including powders, liquids, or impregnated materials.
- Long-lasting protection for months or years, depending on conditions.
Why Choose VCIs?
Vapor Corrosion Inhibitors (VCIs) stand out among corrosion prevention solutions due to their ease of application, flexibility, and proven effectiveness. Compared to other methods like wax, VCIs offer several key advantages:
- Ease of Installation: VCIs are easy to apply, requiring no heating—just simple mixing with potable water and injection through vent pipes, ensuring efficient distribution.
- Broad Compatibility: VCIs work seamlessly with other corrosion prevention methods, such as coatings and cathodic protection, enhancing overall protection strategies.
- Cost-Effectiveness: By extending the lifespan of assets and reducing the need for frequent maintenance, VCIs provide a high return on investment over time.
- Allows Monitoring: VCI effectiveness can be monitored in real time using coupons, ER probes, or UT probes, with the option for remote monitoring units (RMUs). In contrast, wax requires in-line inspection (ILI) runs for evaluation.
- Non-Invasive: Unlike some traditional methods, VCIs do not require disassembly for application, making them a convenient choice for hard-to-reach areas.
- Versatile Applications: VCIs are available in various forms, including films, papers, powders, liquids, and emitters, making them adaptable to a wide range of industrial needs.
- Removability: VCIs can be easily washed out and removed if necessary, offering flexibility for future maintenance or operational adjustments.
- Environmentally-Friendly: VCIs are an environmentally friendly solution for corrosion prevention, offering biodegradable formulations, non-toxic options for sensitive industries, and contributing to sustainability by reducing waste and extending asset life.
- Industry-Approved Solution: VCIs are recognized and approved by leading authorities, including the Association for Materials Protection and Performance (AMPP) and the U.S. Department of Transportation’s Pipeline and Hazardous Materials Safety Administration (PHMSA).
Through our partnership with Zerust® Oil & Gas, MATCOR delivers these benefits with proven products backed by extensive research and industry expertise.
Applications of Vapor Corrosion Inhibitors Across Industries
- Oil and Gas: Protects internal surfaces of pipelines after hydrotesting and safeguards tanks bottoms from localized corrosion. Learn more about pipeline corrosion risks and prevention methods in our Pipeline Corrosion and Prevention—A Comprehensive Guide.
- Manufacturing and Industrial Equipment: Shields components during storage, shipping, or idle periods.
- Marine and Offshore: Mitigates corrosion from saltwater and high-humidity environments.
- Aerospace and Automotive: Protects critical systems like engines and fuel tanks during long-term storage.
- Infrastructure and Utilities: Prevents corrosion in water pipelines, bridges, and utility equipment.
Monitoring and Maintenance
To ensure the long-term effectiveness of VCIs, regular monitoring is essential. Techniques include:
- Coupons: Small metal pieces placed in the protected environment to assess corrosion rates.
- ER Probes: Monitor changes in electrical resistance to track corrosion over time.
- Replenishment: Determined based on environmental conditions and the observed depletion rate of VCIs. Factors influencing replenishment frequency include:
- The rate of leakage through the tank chime.
- Operating temperature and environmental conditions.
- Properties of the substrate, such as sand or concrete.
- The initial amount of VCI chemical applied.
Typically, VCIs provide effective protection for 3–5 years, though some applications may last longer under optimal conditions. Proper monitoring ensures VCIs maintain consistent protection and helps operators identify the appropriate timing for replenishment to sustain corrosion prevention.
VCIs and Industry Standards
Vapor Corrosion Inhibitors (VCIs) are gaining recognition in industry standards as a flexible and effective corrosion prevention tool. While they are often used to complement cathodic protection (CP), they are also being acknowledged as standalone solutions in scenarios where CP may not be feasible.
- API 651 and API 2610: Standards such as API 651 include VCIs as an alternative for situations where CP systems are unsuitable, and API 2610 outlines their use under tank bottoms.
- Regulatory Adoption: Organizations like PHMSA and the State of Florida have endorsed VCIs for their versatility, particularly in cases where CP systems are not functional or economical.
These endorsements highlight the growing recognition of VCIs as a versatile tool for corrosion prevention, whether as a standalone solution or a complement to existing systems like CP.
Independent Studies Supporting Vapor Corrosion Inhibitors
The effectiveness of Vapor Corrosion Inhibitors (VCIs) is well-supported by independent research, including a comprehensive 2018 study published by PRCI (Pipeline Research Council International). This study offers critical insights into the capabilities and limitations of VCIs:
- Effectiveness in Corrosive Environments: VCIs were found to effectively mitigate pitting corrosion in steel exposed to corrosive sand. However, the study noted that VCIs are not as effective as cathodic protection (CP) for reducing pitting corrosion in certain conditions.
- Importance of Proper Application: The study emphasized the need for following manufacturer-recommended concentrations, as inadequate levels of VCIs were shown to be ineffective.
- Monitoring Compatibility: ER probes can be used to monitor the efficacy of VCIs, providing valuable data on corrosion rates and the need for replenishment.
- Compatibility with Cathodic Protection: VCIs are compatible with impressed current cathodic protection systems. However, they can alter the native potential of steel, which must be considered when selecting CP criteria in accordance with NACE SP0193.
For more details, access the full study: PR-015-153602-R01 Vapor Corrosion Inhibitors Effectiveness for Tank Bottom Plate Corrosion Control.
Vapor Corrosion Inhibitor Case Studies: Real-World Success with VCIs
Pipeline Preservation with VCI in West Texas
MATCOR and Zerust® collaborated on a pipeline preservation project in West Texas, injecting over 24,000 gallons of VCI solution into pipeline manifolds. This approach provided effective corrosion protection during construction and harsh environmental conditions.
For more details on how VCIs address pipeline-specific challenges, visit our Pipeline Internal Corrosion Prevention with VCI page.
Casing Repair with VCI
MATCOR conducted a casing repair for a high-pressure natural gas line that had settled, losing contact with its protective casing. The solution included sealing the casing and injecting VCIs through the vent pipe, providing effective corrosion protection without excavation.
Learn more about this project in our Casing Repair & VCI Case Study.
Q&A: Common Questions About Vapor Corrosion Inhibitors (VCIs)
No, VCIs have a finite lifespan. Their effectiveness typically lasts 3-5 years, depending on factors like environmental conditions, application methods, and leakage rates. Regular replenishment is needed to maintain protection, with some applications lasting up to 15 years under ideal conditions.
VCIs can be applied as powders or liquids, depending on the tank type (new,in-service, or under inspection). The method varies based on substrate material (ie. sand or concrete), but long-term replenishment planning is essential to sustain protection.
VCIs are not typically used as a standalone replacement for other methods but are effective for short-term corrosion protection or in scenarios where other solutions are not practical.
Yes, VCIs work well alongside existing methods by addressing localized corrosion in hard-to-reach areas like gaps, crevices, and irregular surfaces. This complementary approach strengthens overall protection.
VCI effectiveness is monitored using coupons, ER probes or UT probes. These tools measure corrosion rates and help identify when replenishment is required. While ER probes track average corrosion rates, they can also infer localized risks like pitting.
VCIs are recognized by standards such as API 651 and API 2610 for specific applications, and they are included in the upcoming NACE TG543 guidelines. Regulatory bodies like PHMSA also acknowledges VCIs as a valid corrosion prevention tool, especially when other methods are infeasible.
Conclusion: The Future of Corrosion Prevention with VCIs
Vapor Corrosion Inhibitors (VCIs) are transforming the landscape of corrosion prevention across industries. From pipelines and storage ranks to marine and aerospace applications, VCIs provide a versatile, cost-effective, and environmentally friendly solution for protecting metal assets. Their ability to adapt to various environments and integrate with other corrosion prevention methods makes them a critical tool for modern infrastructure and equipment management.
Through our partnership with Zerust® Oil & Gas, MATCOR delivers proven VCI solutions backed by extensive research and industry recognition. Whether you’re seeking to enhance existing systems or explore standalone VCI applications, our team is ready to help you develop a customized strategy to protect your assets and reduce long-term maintenance costs.
To get in touch with our team of corrosion experts for more information, to ask a question or get a quote, please click below. We will respond by phone or email within 24 hours. For immediate assistance, please call +1-215-348-2974.
Contact a Corrosion Expert
Can VCI be used in annular space between carrier and casing pipe in road/ railways/ river crossing?
case-I
Each end of annular space between carrier & casing pipeline is sealed with proper end seal.
case-II
No end seal is envisaged in annular space between carrier & casing pipeline .
Dear Madam Nivedita,
I received your question from our posting on VCI.
Absolutely, VCI has been very successfully used on many cased crossings by pumping the VCI into the annular space between the casing and the pipeline. It does require that there be a proper end seal or the VCI will escape out the ends and not have sufficient vapor concentration to be effective.
We have also used VCI successfully for new construction pipelines for the period after hydrotesting and before the pipeline is put in service – this can be a very critical period of time for internal corrosion as the hydrotest water is usually not the best quality and then it can be several months after hydrotesting before the pipeline is put in service – filling the pipeline with VCI is a good corrosion preventative for this application post hydro.
Let me know if we can help you with any VCI applications.
Best Regards
Ted Huck
Director of Manufacturing & QA
MATCOR, Inc.