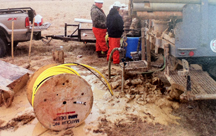
An International Petrochemical Company contracted with MATCOR to review assessment data gathered more than 10 years earlier. MATCOR’s initial findings showed the existing Cathodic Protection System was struggling to maintain criteria. To determine the exact cause of the problems MATCOR launched a comprehensive survey of 20 miles of 26 inch pipeline.
From the initial review of the pipeline, it became clear that the existing Cathodic Protection system did not have the capacity to distribute DC current effectively. MATCOR’s technicians performed Close Interval Surveys (CIS), Pipeline Current Mapping (PCM), and Direct Current Voltage Gradient (DCVG) surveys. In addition, MATCOR took soil samples and had them analyzed, measuring pH, sulfates and sulfides, chlorides and moisture content. The results corresponded with the smart pig runs, which further validated the testing and data analysis. The survey revealed significant coating degradation.
It was clear from the current requirement test results that a new Cathodic Protection System was necessary. The client’s choice was MATCOR’s patented Mini-Deep Anode System, which is very easily installed without disruption to the pipeline.
In all, 15 Mini-Deep Anodes were used to protect 40-plus miles of pipeline and connecting laterals.
MATCOR strategically placed ground beds approximately one mile east and west of the rectifiers. On a new pipeline, each MATCOR Mini-Deep Anode can protect many miles of line, but since these pipelines experienced coating degradation, MATCOR designed the system to protect the existing lines from low structure to electrolyte potentials.
Upon completion of the testing and commissioning of the rectifier and ground bed system, this pipeline system, with associated laterals, was able to achieve -850mV OFF potential throughout its entire length.
The client was concerned that the 100mV criterion would have to be used in certain areas due to poor coating conditions; however, this was not the case. MATCOR achieved complete integrity by incorporating the correct combination of engineering, design, and cooperation from the client.
The Mini-Deep Anodes will protect the system for 20 years or more.