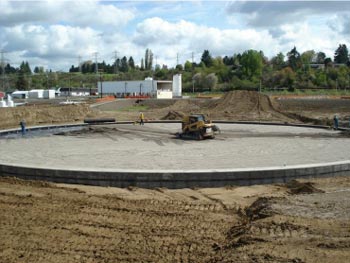
For new construction tank projects and for retrofits of existing tanks, it is common practice to install clean washed sand as the pad upon which the tank bottom is fabricated. The use of oil sand, crushed stone, asphalt, or other materials directly under the tank bottom should be avoided, as these hinder effective tank corrosion protection. This article provides guidelines to the specifications for the sand bedding materials. These guidelines are based on providing a low corrosivity environment compatible with cathodic protection to assure a long service life of the tank bottom.
Economic Considerations
For a typical 150-foot diameter tank using 12 inches of sand bedding the quantity of sand that is required is approximately 17,679 cubic feet of sand which is roughly 883 tons. The cost of the sand, including delivery, is a significant cost and far exceeds the cost of cathodic protection– especially if the sand specifications are quite stringent and require sourcing sand that requires significant transportation. Some consideration can be given to relaxing the sand recommendations, even if that warrants increasing the cathodic protection requirements, should there be a significant cost impact to complying with the sand specifications – consult your cathodic protection designer.
Recommended Sand Properties
The table below summarizes the recommended sand properties to support aboveground storage tank corrosion protection.
Property | Recommended Value |
Resistivity (ohm-cm) | 20,000 – 100,000 |
pH | > 6.5 |
Chlorides (ppm) | < 10 |
Sulfates (ppm) | < 200 |
Sulfides (ppm) | < 0.1 |
Particle Size | 100% pass through #4 Sieve |
Soil Resistivity
The best proxy for determining corrosivity of sand materials is the electrical resistivity of the sand. Clean washed sand typically has resistivity values more than 20,000 ohm-cm and in some cases can exceed 100,000 ohm-cm. The higher the resistivity of the sand, the lower the corrosivity of the sand; however, when designing cathodic protection, the higher the sand resistivity the greater the impact on the overall system resistance and the electrical power required for the cathodic protection system. API Recommended Practice 651 Cathodic Protection of Aboveground Petroleum Storage Tanks provides the following table classifying resistivity of soil/sand.
Resistivity Range (ohm-cm) | Potential Corrosion Activity |
<500 | Very Corrosive |
500 to 1000 | Corrosive |
1000 to 2000 | Moderately Corrosive |
2000 to 10,000 | Mildly Corrosive |
>10,000 | Progressively less corrosive |
Soil Resistivity Testing Methods »
Sand pH Range
Measuring pH indicates the hydrogen ion content of a soil. Corrosion of steel is fairly independent of pH when it is in the range of 5.0 to 8.0. The rate of corrosion increases appreciably when pH is < 5.0 and decreases when pH is> 8.0. pH may be determined in accordance with ASTM G 51 or equivalent
Chlorides
Chlorides will affect the resistivity of soil, and act as a depolarizing agent which will increase the current requirement for cathodic protection of steel. Pitting corrosion on steel can begin at chloride levels of 10 ppm. Chloride content may be determined in accordance with ASTM D 512 or equivalent.
Sulfates
Sulfate levels >200 ppm frequently indicate high concentrations of organic matter. Sulfate content may be determined in accordance with ASTM D 516 or equivalent.
Sulfides
Sulfide levels > 0.10 ppm may indicate that sulfates have been reduced by bacteria. Sulfide content may be determined in accordance with EPA 0376.1 or equivalent.
Particle Size
The sand bedding material should be clean of rocks, clumps and other debris and for clean sand capable of passing through a #4 sieve, for washed river sand an alternative acceptable particle size is 100% pass through a 3/8” sieve.
Sand Depth of Cover
For new construction tanks, the typical design is to provide a minimum of 12 inches (30 cm) of sand cover; however, for tank bottom retrofits it is quite common to provide 6 inches of sand (15 cm) for double bottom installations or for applications where the existing bottom is removed, and the top layer of the underlying soil foundation is being removed.
Very informative and straight to the point.
Thank you Chris!
We are having a problem with low readings on our potential meter when checking UG Propane tanks at one location. The tanks have two feet of sand beneath and then backfilled with sand around and on top, maybe 3 inches of top soil. We get ok readings at the end of tanks location about 6 feet away but very low readings between tanks. Can the sand cause this? And what is needed to fix if that is the case?
Dear Manny,
Thanks for visiting our site and for your question. Low potentials are indications that you do not have sufficient cathodic protection to meet established criteria. There are several factors that can result in low potentials, and these need to be evaluated based on the circumstances of your specific application. We strongly encourage you to engage a CP professional to review the low potentials that you are reading for the appropriate recommendations and remediation.
If we can be of assistance in this project, please let us know.
Best regards,
MATCOR, Inc.
A customer insist in using sand oil (sand + diesel or bunker) pad for their AST bottom. How can I show customer that is a bad decisión.
Dear Cesar,
Thank you for your inquiry. The corrosion industry has moved away from recommending the use of oiled sand as a bedding material to help prevent corrosion of tank bottoms. The oil-sand mixtures have been found to create more issues than they solve by not providing an effective dielectric non-conductive tank coating that does have enough non-conductive material to shield the effective flow of cathodic protection current.
NACE SP-0193-2016 Application of Cathodic Protection to Control External Corrosion of Carbon Steel On-Grade Tank Bottoms states:
“5.6.1.7 Oiled tank pad materials shall not be used for new construction.”
API 651 has similar language.
We hope this is helpful. Let us know if we can further assist.
MATCOR, Inc.
What is the ration of sand to bitumen
Hi Patrick,
Thank you for your inquiry. MATCOR does not recommend mixing Bitumen with sand. This is a poor practice that has been proven to cause shielding issues that adversely affect the application of cathodic protection.
MATCOR, Inc.