At the June AMPP Arizona Chapter Meeting, MATCOR’s Ted Huck delivered a powerful and eye-opening presentation titled “The Race to Artificial Intelligence (AI) Supremacy and How it Threatens Our Pipelines.” The session highlighted the connection between the global competition for AI dominance, skyrocketing energy demands, and a growing threat to pipeline integrity across the United States.
If you missed it, here’s a recap of the key insights and takeaways.
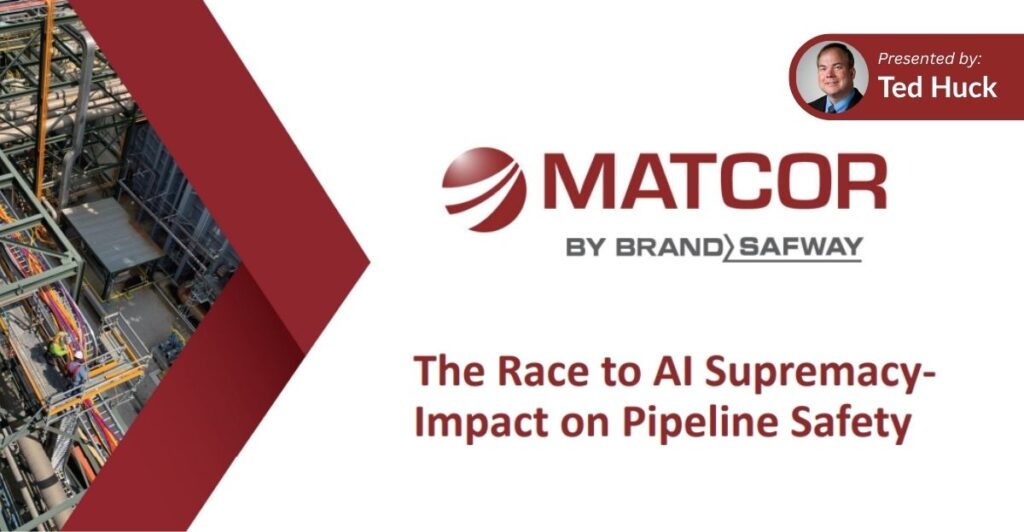
The AI Boom is Power-Hungry
Artificial intelligence isn’t just changing technology—it’s reshaping our entire power infrastructure. Data centers, driven by AI, cloud computing, and social media storage, are expanding at an unprecedented pace. According to Huck, these facilities already consume 4–5% of U.S. electricity, and that number could jump to 15–20% within five years.
The global race among countries to scale AI capacity is essentially a race to build and power massive new data centers. In the U.S., natural gas—already accounting for about 45% of electricity generation—is expected to drive most of the growth, as coal continues its steep decline and nuclear struggles to rebound. In contrast, other countries are doubling down on coal, approving over 100 gigawatts of new coal-fired capacity. They are also building coal plants faster than the U.S. can build gas plants—giving them a potential edge in scaling data centers faster.
More Power = More Problems
With rising energy demand comes the need for more power plants and thousands of miles of new high-voltage transmission lines. Many utilities are expanding capacity not only by building new lines but also through “reconductoring”— upgrading existing lines to carry twice the electrical load with no major visible infrastructure changes.
What does this mean for pipeline operators?
You won’t get a phone call when the power load in your right-of-way doubles.
As Huck emphasized, power companies are under no obligation to inform you when they increase the electrical load on transmission lines. One MATCOR client installed a mitigation system just three years ago—only to discover massive increases in AC interference due to a nearby data center and reconductor line. Their existing system was suddenly inadequate, and no one warned them.
Co-location is the New Norm
Today’s utility corridors are getting more crowded. Pipelines and power lines are increasingly co-located, sharing the same physical space. This increases the risks of:
- Conductive coupling from fault currents
- Electromagnetic induction from steady-state AC loads
- Elevated AC current densities that accelerate corrosion
Huck warned that even pipelines with few defects can experience high localized current densities—especially if CP systems aren’t designed to maintain uniform protection across high-risk areas.
The New Standard: NACE SP21424
A major portion of the presentation focused on the implications of NACE SP21424, the evolving standard for AC interference and corrosion.
Unlike previous guidance, SP21424 links allowable AC current density to measured DC current density, requiring a shift in how pipeline integrity is monitored and designed. It introduces several new expectations:
- Measurement of DC current density, something rarely done before
- Use of coupons and smart test stations to track time-weighted averages
- Immediate mitigation installation for new pipelines in AC-influenced areas
- Separate CP systems in areas of high risk for tighter control and faster response
Operators are now expected to collect, store, and interpret data over time—not just take snapshots during annual surveys. And yet, key terms like “time-weighted average” and “representative monitoring periods” remain undefined, placing the burden on operators to proactively set thresholds within their integrity programs.
Smart Monitoring = Better Protection
To keep up with rising threats, Huck urged operators to:
- Install more CP stations at lower outputs to reduce high DC current density
- Implement dedicated CP systems for AC-influenced zones
- Upgrade test stations with dual AC/DC coupons and remote monitoring
- Define your own time-weighted thresholds in advance—don’t wait for regulators
With widespread reconductoring, new power plants, and surging energy demands, these recommendations aren’t just best practices—they’re becoming essential for risk mitigation.
Bottom Line: AC Mitigation Can’t Wait
“The power utility isn’t going to notify you,” Huck reminded attendees. “It’s on operators to monitor, detect, and respond to changing conditions—before they become serious problems.”
The growth of AI isn’t just a tech trend. It’s a pipeline risk multiplier.
As energy demands surge, so do the risks to pipeline infrastructure—especially from AC interference. Learn more about AC mitigation and explore MATCOR’s full range of pipeline AC mitigation services.