Exothermic welding and pin brazing are two methods to connect a cathodic protection system to the protected steel structure. These connections route back to the rectifier to complete the circuit for an impressed current cathodic protection system. Or they connect to the anode lead cable in a galvanic anode system. They are an essential part of any cathodic protection system.
Exothermic welding and pin brazing cathodic protection connections resulted from historical needs in the railroad industry. In addition, both have a long history of use in the cathodic protection industry.
MATCOR has the experience and capability to use either connection technology depending on the client’s specifications or requirements. In the absence of a customer preference, MATCOR generally defaults to pin brazing for CP applications.
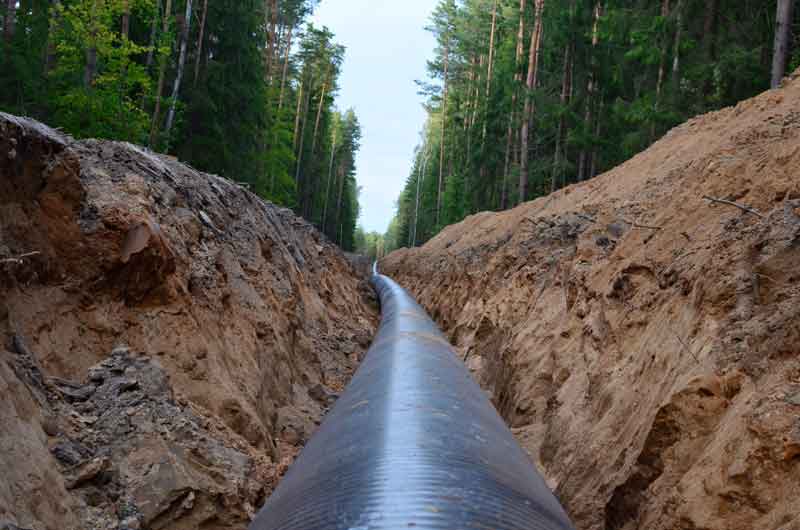
Exothermic Welding for CP
The older of the two technologies is Exothermic or Thermite welding. More prevalent in United States specifications, this technology utilizes the heat generated from the reaction when you ignite a mixture of Aluminum powder and Iron Oxide III (ferric oxide Fe2O3). The resulting reaction is vigorously exothermic, generating temperatures more than 2000 C – sufficient to create molten iron.
Initially developed by German Chemist Hans Goldschmidt in 1893, exothermic welding connected steel rails on the Essen train line. In the 1930s, the technology gained widespread use for connecting bonding cables to railroad ties. This was thanks to the efforts of Charles Cadwell, a physicist for the Electric Railroad Improvement Corporation (ERICO.)
The Cadweld connection process has changed very little over time. It involves cleaning the structure surface down to the bare metal and laying the connector attached to the structure in a graphite mold. Next, you place an appropriately sized cartridge containing the aluminum powder and ferric oxide ready for igniting in the mold. Finally, using an ignitor sparks the reaction. As a result, an iron slug melts and flows over the copper conductor, welding it to the steel surface.
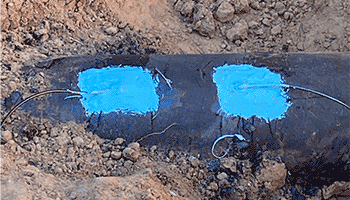
Pin Brazing for CP
Like exothermic welding, the railroad industry developed the second standard cable-to-structure technology—pin brazing.
In Sweden in the 1950s, high heat from thermite welding caused grain growth in the copper cable. As a result, connections to the rails were subject to fatigue failures from cyclical stresses associated with the movement of the rails as trains passed.
To solve this issue, the railroad industry developed lower-temperature joining technology using brazing. Brazing uses a range of silver-based filler metals to achieve the bond. These filler metals have a melting temperature between 620 and 970 C – well below the temperatures reached during exothermic welding.
Commonly specified in European standards, the pin brazing process has remained fundamentally the same since the 1950s, with some refinements to the equipment.
The pre-assembled welding pin and the pin brazing gun are the keys to pin brazing. The pin consists of a stud with a defined amount of flux encapsulated in the brazing metal. When you press the trigger, current flows through the pistol via the pin to the steel pipe. At the same time, an electromagnet is energized, drawing the pin holder and pin away from the steel surface, forming an electric arc. The arc heats the steel and starts to melt the tip of the pin. As a result, it causes the flux to melt and flow onto the steel. The electromagnet de-energizes when the current flow ceases, and the spring forces the molten stud onto the fluxed pipe surface. With the arcing stops, solidification is very rapid.
Comparing Exothermic Welding and Pin Brazing for Cathodic Protection Connections
Safety
Both methods are safe procedures when trained personnel follow the correct procedures. Neither method poses any environmental threat, although users should be sure to properly store and handle the thermite powder charges. For thermite welding, the process can be sensitive to moisture which could vaporize on contact with the molten iron slug. As a result, the potentially dangerous hot metal can be spat out of the mold. For this reason, you should conduct the pin-brazing process in damp environments and offshore applications.
Cathodic Protection Connection Reliability
Both connections have been used extensively and are widely accepted in cathodic protection. Unfortunately, no published data detailing the reliability of either connection technology exists, and reports of Cathodic Protection connection failures are infrequent and anecdotal. Lab testing on tensile load indicates that pin brazing is a slightly stronger bond; however, the loads at failure far exceeded any load possible in regular service. Nevertheless, both techniques will provide reliable, low-resistance connections when properly performed.
Metallurgical Effects
Both processes are thermal and will affect the metallurgical condition of the pipe. Many piping codes typically advise that the design consider the impact of any changes in the parent metal due to localized heating during the attachment process. Microhardness testing has shown that both connections are safe for the normal range of carbon steel pipe; however, some consideration must be given to thin-walled structures. Pin brazing results in lower temperatures and greater process control and should be considered for all thin-walled steel and alloyed piping.
Effects of Cathodic Protection Connections on Internal Coating and Fluids
Using thermal bonding to the exterior pipeline wall of a pipeline filled with highly flammable hydrocarbons requires some consideration. In addition, where internal coatings exist, it is reasonable to question whether or not thermite welding or pin brazing might damage the interior coating. Based on testing, the inner wall temperature rises more with thermite welding than with pin brazing; however, neither method’s results were sufficient to give any reason for concern.
If you need assistance with a cathodic protection assessment, please contact us. We will respond by phone or email within 24 hours. For immediate assistance, please call +1-215-348-2974.
Contact a Corrosion Expert